CATEGORIES
FEATURED PRODUCTS
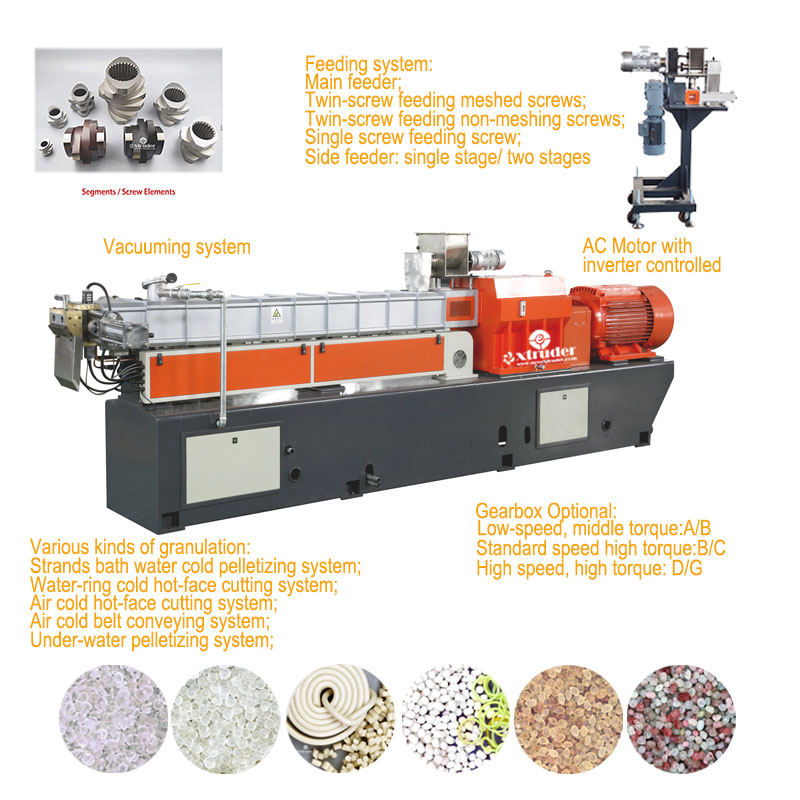
SHJ Series of Plastic modification Twin-screw extruder
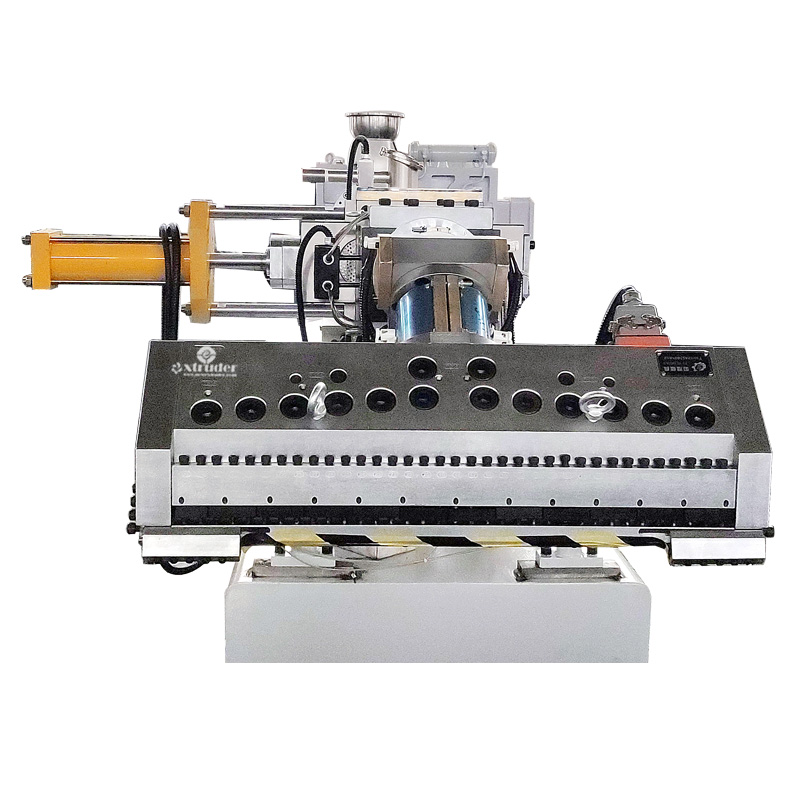
Plastic Sheets Extruder PE PP PVC PBS PLA Sheets Machine Lines
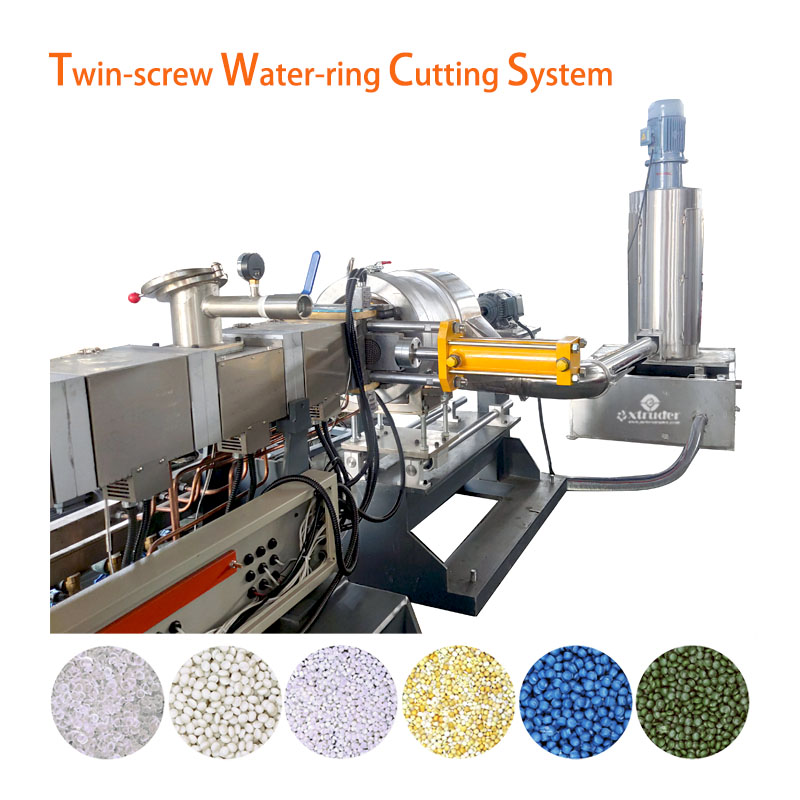
WATER-RING PELLETIZING SYSTEM TWIN SCREW PLASTIC POE EXTRUDER
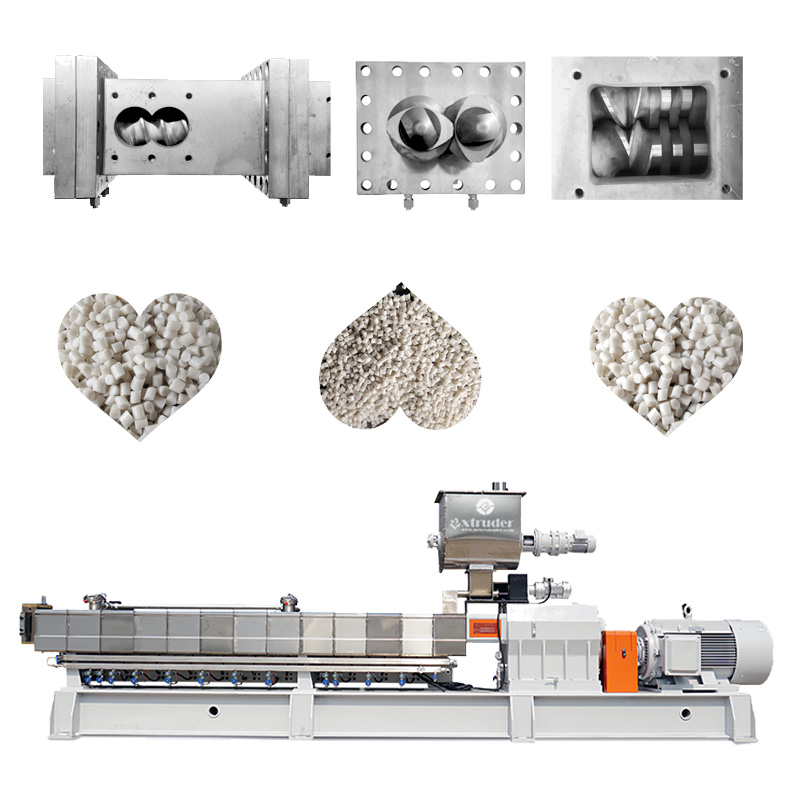
EVA Titanium powder added Photovoltaic PV membrane granules extruder large output capacity plasitc extruder
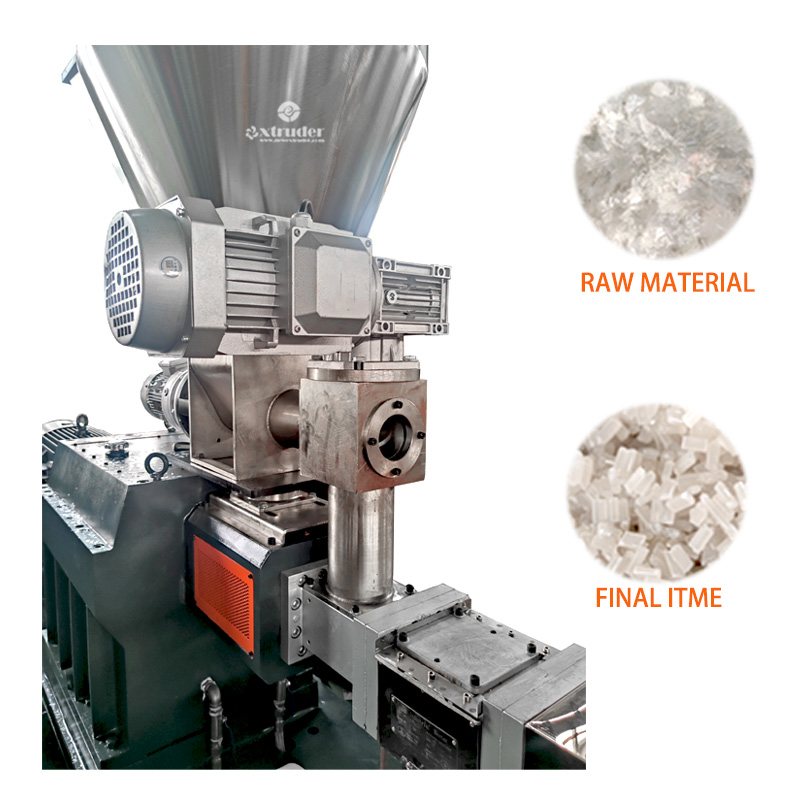
Recycling plastic regranulation extruder machine PE PP PET ABS recover granulation system recycling and reusing extruder
SHJ Series of Plastic modification Twin-screw extruder
SHORT DESCRIPTION:
Kosin extrusion machinery Co. supply you not only co-rotating twin-screw, tri-screw plastic extruders for color masterbatch, filling masterbatch, Bio-Degradable particles, Engineering, functional plastic granules making, but also support you various kinds of plastic sheets extruder, such as PE, PP, PVC, PET, PBS, PLA, etc added starch powder( corn starch, cassava starch and etc.) for degradable sheets making for disposable products made.
- Product Detail
- Our machine can process the following materials:
- Product Tags
Application for all kinds of plastic modification extruders:
Color Masterbatch;
Filler Masterbatch
Biodegradable Plastic granules and sheets: PLA, PBS with starch;
Plastic sheets: PE, PP, PVC with starch powder or calcium carbonate powder,
PET transparent sheets, etc.;
Recycling film and bottom chips recovery granulation;
Elastomer granules and Elastomer modification particles;
Engineering plastic modification granulation
Functional masterbatch: Anti-ageing, Anti-ultraviolet, ultraviolet light absorber, Anti-static and etc.;
Reactive extrusion project: TPU, TPR, TPE, and other plastic and rubber materials
Fire retardant masterbatch, flame resistance masterbatch;
PET recycling granulation: PET waste film and PET bottle crushed or cracked chips;
LGF (Long Glass Fibre) reinforced particles and Short Glass Fiber reinforced particles (needing side-feeder).
Thermoplastic Elastomers
SHJ Series Co-rotating Twin Screw Plastic Extruder can make following different kinds of plastic granules & particles: | Twin-screw Plastic Extruder has Different kind of Pelletizing method |
SHJ SERIES OF TWIN SCREW PLASTIC EXTRUDER
|
VARIOUS KINDS OF THE PARTICLES/GRANULES
|
Features & Advantages i
(1) With the same direction parallel double shafts and twin-screw segments combined by a special design, the final plastic granules quality will be good and match the customers’ demands and requests. The screw segment combination could be adjusted by different plastic materials and different clients’ requirements.
(2) Both screw and barrel are combined. There are many kinds of screw elements, including conveying elements, kneading segments, shearing segments, reverse screw segments, and pressurized screw elements, which play different roles. According to the needs of material processing, various screw elements (screw segments) are combined by building blocks, and through optimization design, they can match and adapt to the processing of various process formulated plastic materials.
Features & Advantages ii
(3) The mixing, shearing, and kneading segments block have a geometric shape that has a spiral of the spiral block and the same direction of rotation, so that the spiral has a good material distribution and mixing ability, suitable for mixing operations. After the material enters the barrels after softening and melting, the twin screw in the meshing position in the opposite direction, a screw will pull the material into the meshing gap, and another screw will push the material out of the gap, so the material is transferred here by a screw to another screw, as “∞” movement. This movement has a large relative speed at the meshing position, which is very conducive to the mixing and homogenization of materials. Moreover, the gap in the meshing area is very small, and the speed of the thread and groove at the kneading point is opposite, which has a high shear effect, to achieve the uniform plasticization effect.
(4) The materials are melted in the barrels’ side by the barrels’ heaters heating, in the meantime, the materials will go ahead by the screw segments and shafts co-rotating (two shafts with screw segments rotating) the twin screw extruder is a dynamic reactor with reactive capacity. A series of chemical reactions, such as polymerization and grafting. Reactive extrusion processing is mainly used for the polymerization of monomers or oligomers: addition polymerization, polycondensation, free radical polymerization, and copolymerization; degradation of polyolefins and Controllable crosslinking; Graft modification of polymer: polar grouping of polymer or functionalization to achieve the purpose of material modification and preparation of compatibilizer; Forced blending modification of various materials. It also includes physical modification of materials, such as filling, mixing, toughening, and strengthening.
Twin-screw Plastic Extruder has Different kind of Pelletizing method:
Strands bathing water cold pelletizing system
|
Strands Air cooling belt conveying system
|
Water-ring cold hot-face cutting system
|
Air–cooling hot-face cutting system
|
Underwater pelletizing system
|
PVC Cable extrusion group
|
Sheet extrusion machine line:
|
Triple screw extruder machine
|
Process |
Representative materials |
Mixing nature-changing |
PE,PP,PS+SBS,PA+EPDM,PP+NBR,EVA +Silicon rubber, etc. |
PE,PA,PC,CPE+ABS(alloy),PBT+PET,PP+ PE etc. |
|
Filling nature-changing |
PE,PP,EVA, etc.+ Calcium carbonate, talcum powder, titanic powder ABS,PC,PS, etc.+ aluminum hydroxide, magnesium hydroxide, antimony oxide. |
PP,PA,ABS +ferrous powder, sulphuric powder ceramic powder |
|
Functional machine pellets |
PP,PA,ABS,PBT, etc+ anti-burning agent and other auxiliary agents: combustion-supporting machine pellets |
PE,PP,PS, etc+ starch: de-composing machine pellets |
|
PE+ fog-preventing dipper, stabilizer: dual-prevention machine pellets |
|
PE,EVA=ABS etc+ carbon black: black machine pellets |
|
Colored machine pellets |
PE,PP,ABS,AS,PA,EVA,PET +pigment and auxiliary |
Intensified glass fibers and carbon fibers |
PP,PBT,ABS,AS,PA,PC,POM,PPS,PET etc.+ long fibers, small fibers, carbon fibers, crystals and so on, etc. |
Various cables |
HDPE,LDPE,LLDPE,MDPE,EVA,PVC,PP, etc. insulating cables,coatings, PE peroxide silicon alkyl crossing cables: radialization crossing cables |
Special materials |
EVA heat-melting glue, polyurethane, fluorine rubber, fluorine plastics, PP cigarette filtering material and TPR sole material |
Reaction extruding |
Poly-amide condensate, poly-amide melting polymerization, poly-amide polythene-adding, poly-carbonate condensate, etc. |
Exhausting and volatilization |
Polystyrene oxide, high-absorbing resin, chlorine sulphur polyethylene |
Powder paint |
Polyester, ring oxide, lactide, polyurethane, acrylate |